Laser printing from nanoparticles opens a window into the world of flexible electronics.
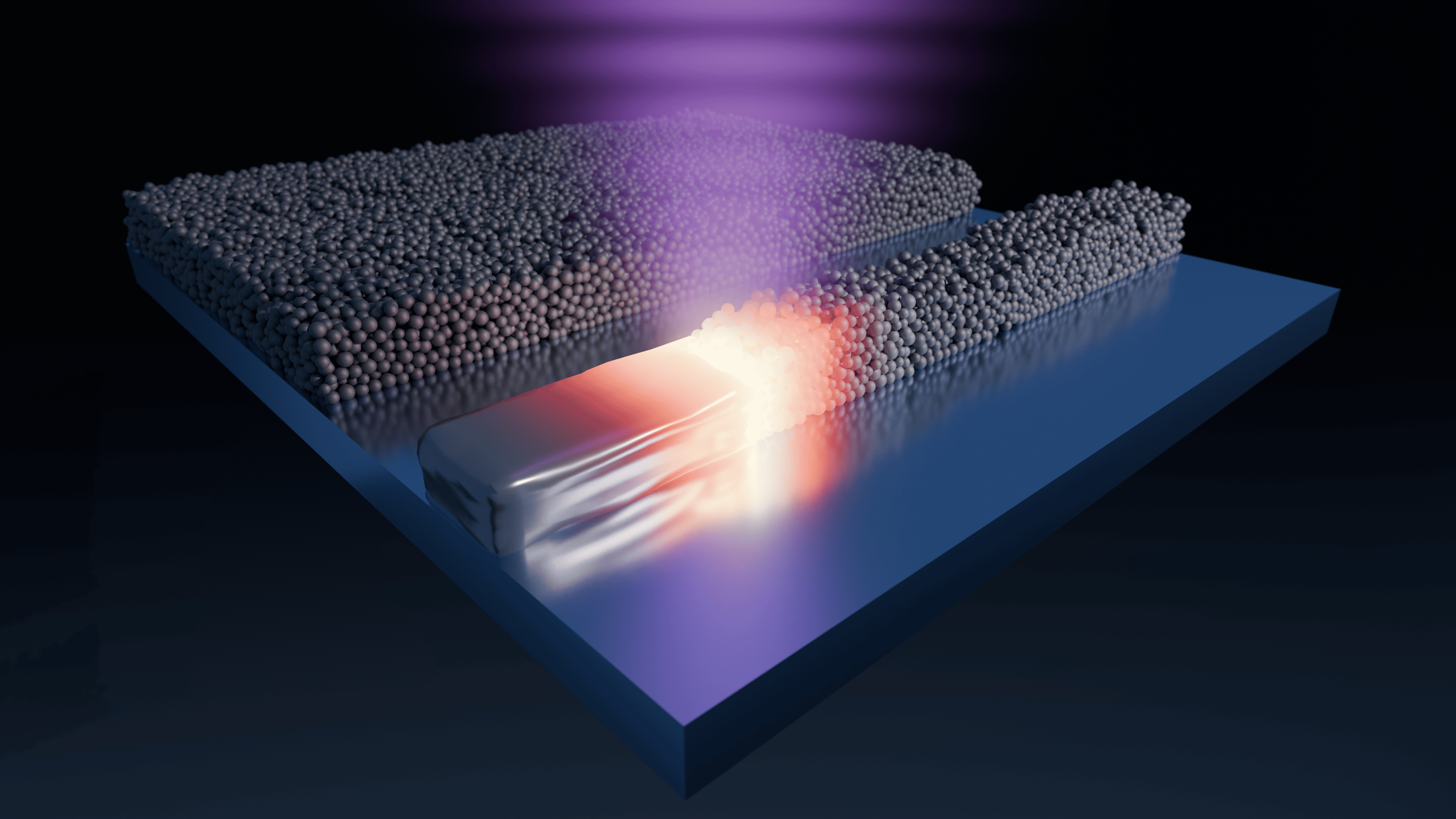
Scientists from the Faculty of Science at the University of South Bohemia have developed a unique method for printing metal from nanoparticles, enabling the combination of sintered and nanoparticle structures within a single product. Additive manufacturing technology has proven effective at the macro scale for rapid prototyping, custom development, and creating porous structures. Metal printing technology at the micro and nanoscale opens possibilities for applications in electronics, optics, and medicine—imagine, for example, a custom implant with printed conductors and sensors.
Standard metal printing technologies using laser sintering rely on grains tens to hundreds of micrometres in size, roughly the thickness of a human hair, which is mechanically placed on a substrate and sintered at temperatures near the material’s melting point, naturally limiting print resolution. These limitations can be overcome by using smaller grains—nanoparticles. But how can such nanoparticles be produced and evenly applied to a substrate while preventing oxidation?
The research team has shown that this is possible by combining selective laser sintering with gas aggregation of nanoparticles. This nanoparticle preparation technology can be imagined similarly to the formation of rain. First, a saturated vapour is created, which then condenses into raindrops that fall to the ground. The scientists from the University of South Bohemia can replicate this with metals, using high vacuum and low-temperature plasma to generate a beam of nanoparticles, objects 1,000 times smaller than the diameter of a human hair.
In the nanoscale world, matter behaves entirely differently. For instance, a silver metal nanoparticle is much smaller than the wavelength of light. When such a nanoparticle is illuminated, its electrons oscillate, and as a result, a single layer of such nanoparticles absorbs about half of the incident light. Moreover, the sintering temperature drops from 962°C to 200°C. This can be advantageously used not only for sintering structures at lower laser power but also for their easy evaporation with high laser power.
In simple terms, a metal target is installed in the device, and when the power supply is turned on, a substrate for printing is placed into the nanoparticle beam and illuminated by a laser programmed to print a given structure that combines nanoparticles and sintered metal with resolution limited by the wavelength of light, not particle size.
The developed technology has been tested for printing micro-mirrors, micro-wires made of nanoparticles or sintered metal, and even the logo of the Technology Agency of the Czech Republic as a thank-you to the funder of the research. The scientists hope that in the future, the technology could assist in prototyping sensors and flexible electronics, especially for healthcare applications.
This unique device and method were developed at the Faculty of Science at the University of South Bohemia, specifically the Department of Physics (Laboratory of Nanomaterials Physics led by Jiří Kratochvíl), the Department of Chemistry (Laboratory of Single Molecule Spectroscopy led by Tomáš Fessl), in collaboration with the Czech Academy of Sciences (Electron Microscopy Laboratory led by Marie Vancová). The technology was selected as a finalist in the national Transfera competition, patented, and published in the prestigious scientific journal Nano Letters by the American Chemical Society, with the editorial team selecting it for the front cover of the journal issue (https://pubs.acs.org/doi/full/10.1021/acs.nanolett.4c03131).
Contact: RNDr. Jiří Kratochvíl, Ph.D. (